01
Vacuum Drying Oiling Equipment
It combines our company's rich experience in transformer production and accumulated expertise in this field.
Mainly used for drying and oiling oil-immersed transformers, amorphous alloy transformers, reactors, and capacitors.
During the drying process, the equipment continuously changes the pressure in the drying tank to ensure that the product is heated evenly, removes evaporated moisture in a timely manner, and prevents the iron core from rusting. Progressive drying method reduces product deformation and ensures thorough drying.
The equipment has a reasonable structure and process. Compared with traditional vacuum drying methods, the drying time is reduced by about 30-45%. It is a reliable, efficient and energy-saving equipment with a fully automatic oil filling system, and the oil volume setting is quick and convenient. We provide transformer technology for the drying and oil filling treatment of electrical products for oil-immersed power transformers below 35KV (optional 35KV and 10KV).
Main technical features of the equipment: The equipment has a carefully designed vacuum system, and sufficient condensed water is released in the low-temperature condenser, which effectively avoids moisture contamination of the vacuum pump during the drying process.
During the heating process, the pressure in the vacuum tank is reduced to a certain value according to the temperature cycle of the product, creating the most suitable conditions for the evaporation of water in the product's insulation layer and ensuring the rationality of the evaporation process during the heating process. drying process.
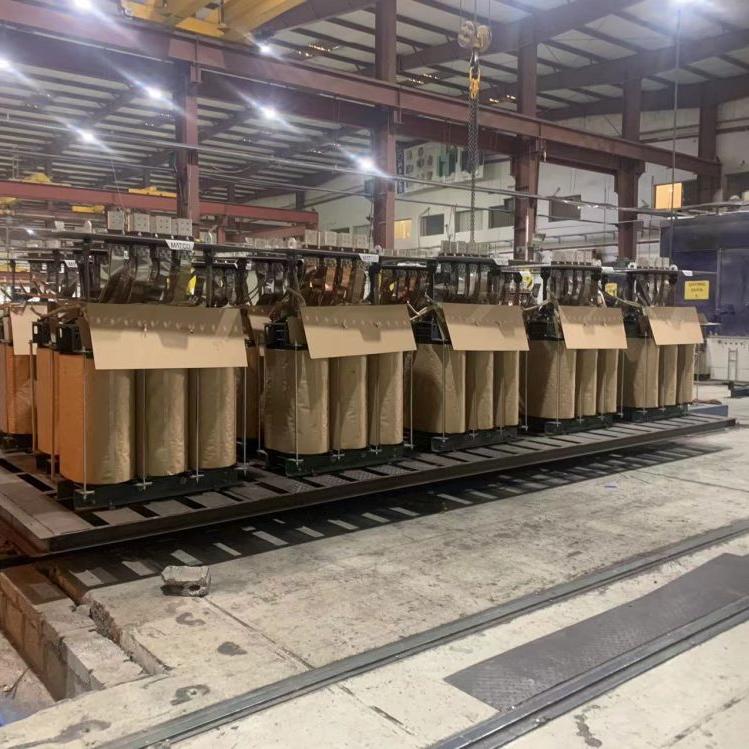
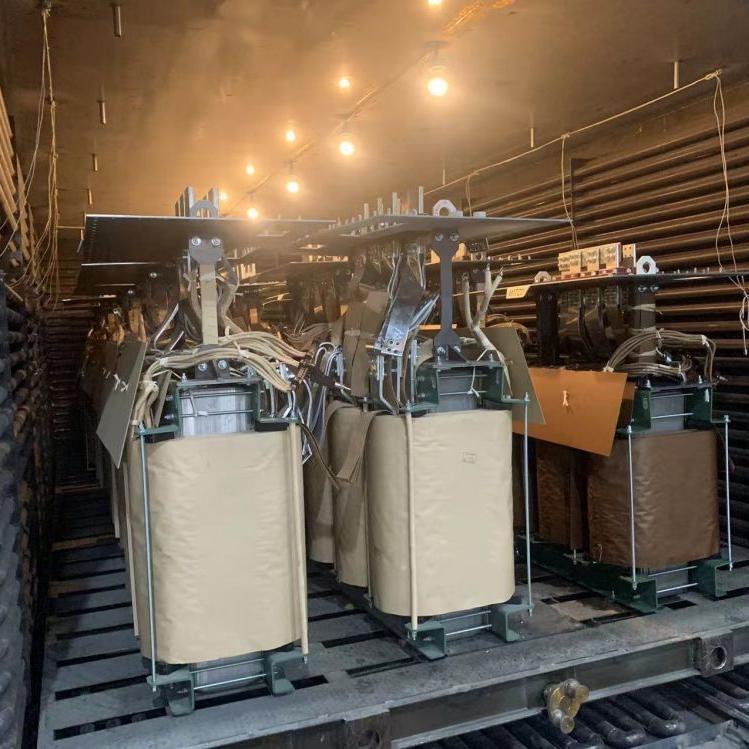
During the heating process, the pressure in the vacuum tank is reduced to a certain value according to the temperature cycle of the product, creating the most suitable conditions for the evaporation of water in the product's insulation layer and ensuring the rationality of the evaporation process during the heating process. drying process.
The equipment is adjusted according to the pressure swing drying process, effectively solving the problem of iron core rusting during the drying process. The equipment automation level and processing technology have reached domestic advanced standards, ensuring that product quality is at the leading level in the industry.
The oil filling process is carried out under full vacuum, and the oil is automatically and accurately filled after drying to ensure reliable product quality.
The equipment adopts a three-stage vacuum pump system, with an empty tank ultimate vacuum of 50Pa and a leakage rate of ≤0.5mbar·l/s, ensuring a high-purity and high-vacuum environment.
An oil-gas separation collector is installed between the vacuum unit and the vacuum tank to condense and recover a portion of the insulating oil, thereby minimizing and reducing the pollution of the vacuum system by the insulating oil.
Vacuum drying and oiling tank doors and tank lid flanges are manufactured according to vacuum equipment standards to ensure the durability of the flanges.
All oil injection pipes and accessories are made of 304 stainless steel.
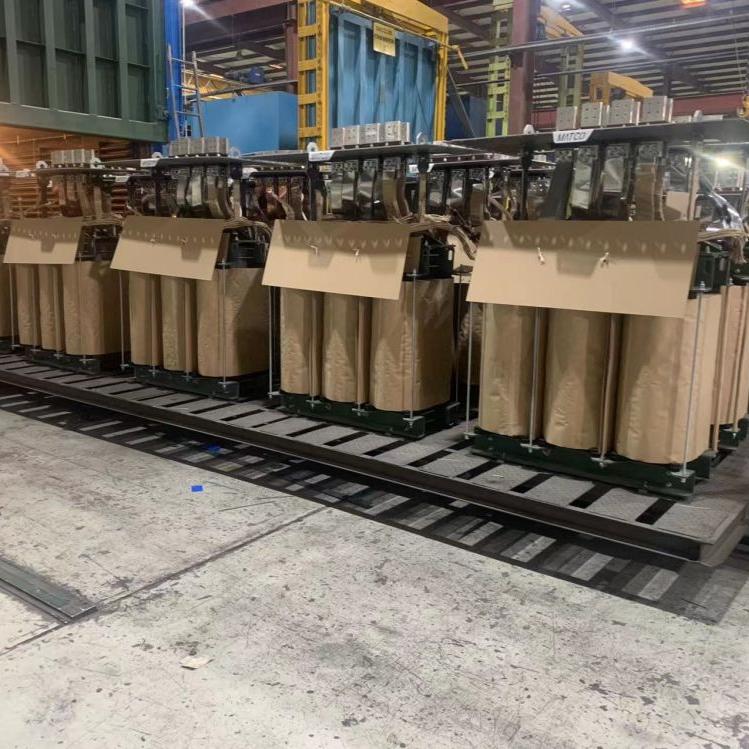
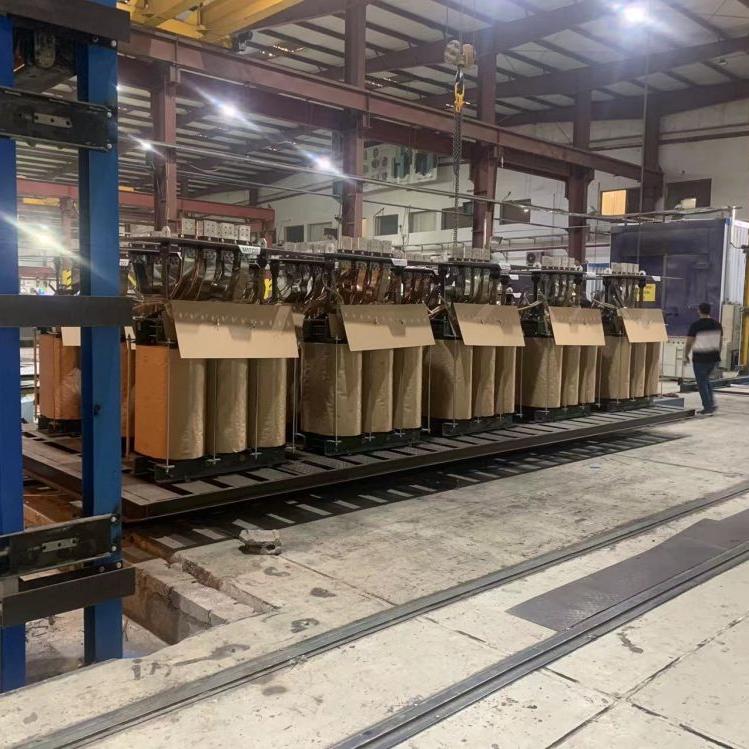
An appropriate number of oil injection branch pipes enter the oil injection tank through flanges.
Each group of branch pipes can be connected to the product through appropriate pipelines to facilitate qualified insulating oil to enter the product.
The oil injection system is equipped with a turbine flow meter, which is used to preset the total oil injection amount of each branch. When the preset oil injection amount is reached, the oil inlet valve closes.
Each branch is also equipped with a manual stainless steel control valve to control the oil injection flow, thereby controlling the oil injection speed.
The high-end control system uses Siemens PLC as the main control unit, and the operating system can realize automatic control of vacuuming and oil filling during the process.
Including temperature overheating alarm prompts, automatic gas cutoff protection, alarm prompts, etc.
The equipment is a single door with vacuum and oil filling functions, and the maximum weight can reach 30T in one operation.
Under vacuum conditions, a single oil filling valve can be used to achieve automatic quantitative oil filling or manual oil filling.
The operation of the equipment is controlled by buttons on the control panel, including door switches, vacuuming, manual/automatic oil filling, etc., and is equipped with complete safety protection devices.